Learning by Doing
Interview with Francisco Mangado and Andrea Deplazes
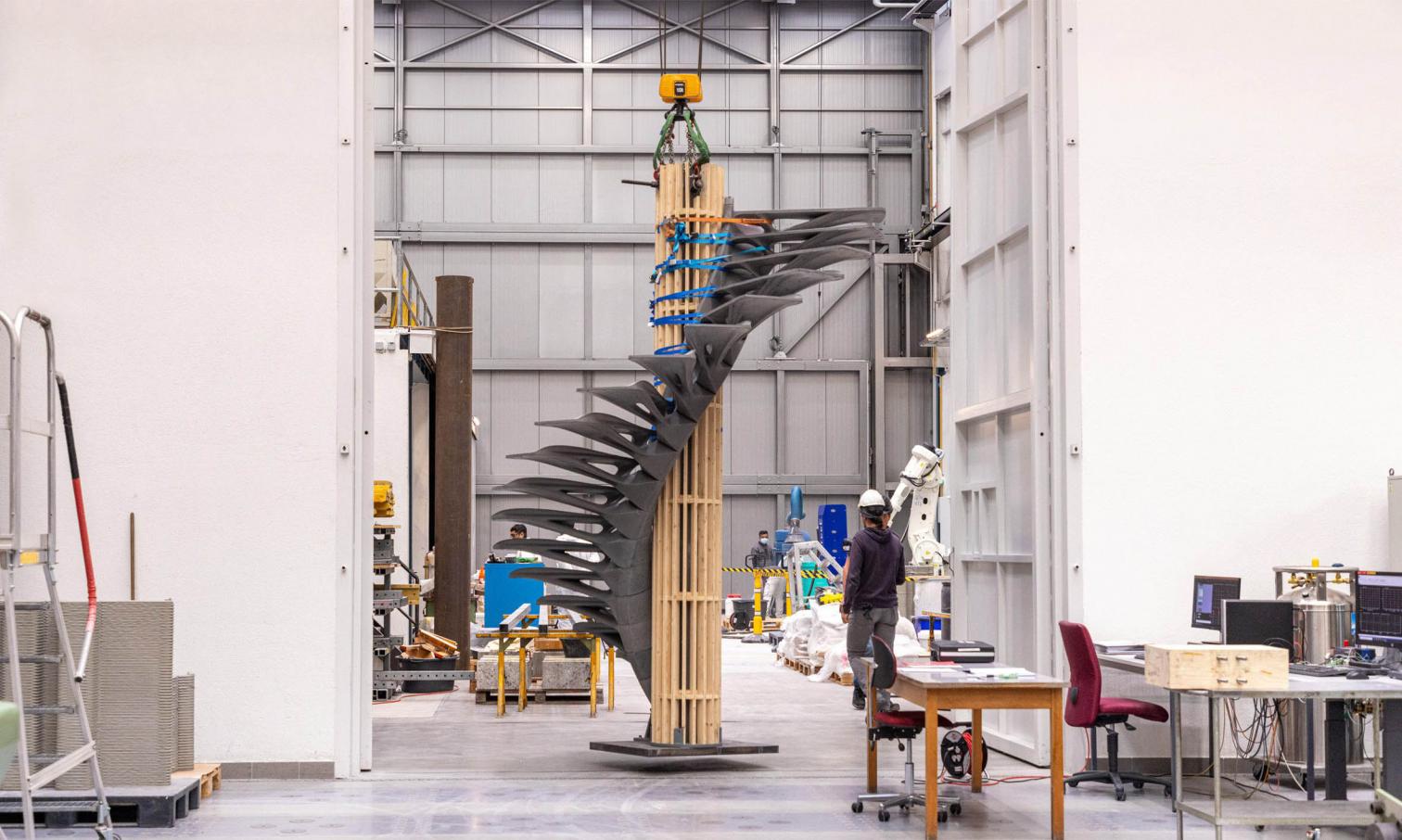
Modern architecture wanted to be industrial; today's architecture also wants to be industrial. But in a different way.
In the convulsive and promising times of the Modern Movement, the ‘factory,’ with its powerful chimneys and endless production lines, was the image in which diverse and complementary programs crystallized. On the one hand, the factory was seen as the best example of what was to come: the new functional but at the same time sublime and perhaps monumental architecture, which would no longer respond so much to the artistic composition of the architect as to the rational calculation of the engineer. On the other hand, the factory was seen as the temple of measurement and prefabrication: the place where the ‘standard’ needs of the ‘type’ were met, and where objects were assembled in parts in that neat and efficient manner that many dreamed of extrapolating to architecture. Hence the factory was also seen as the temple which, in its mechanical ugliness, would make it possible to efficiently meet social needs, especially those of decent and cheap housing, so pressing in a period marked by migration from the countryside to the city. It is therefore not surprising that the factory also functioned as the most intuitive symbol of the new times, of that productivist and partly revolutionary Zeitgeist which from the beginning was associated with a term then considered almost an article of faith: ‘progress.’
‘Progress,’ ‘economy,’ ‘prefabrication,’ ‘standardization,’ ‘function,’ and ‘calculation’ were some of the fundamental words of this heroic period in which architects, with greater or lesser rhetoric, approached factories with enthusiasm. A period that time revealed to be contradictory, because of the promises, the impetus, the initial fires, only ashes remained. On the one hand, the ashes of ‘hard’ prefabrication, which, especially in the socialist countries of the 1960s and 1970s, proved efficient in the ‘big numbers’ but gave rise to architecture of very low quality and poor reputation. On the other hand, the ‘ashes’ of ‘soft’ industrialization which, in the capitalist countries, encouraged a construction model rooted in craftsmanship but made up of catalogue elements (standardized steel sections, sandwich panels, aluminum joinery, prefabricated steps, modular cupboards). In both cases, the result was disenchantment and confusion. Disenchantment at the failure of the modern project, in which many thought they saw the best opportunity to reconcile, forever, industry and beauty. And confusion as to the path to be taken, because, come the nineties, there were many industrialization options available: closed, open, total, partial, completely prefabricated or the hybrid-craft, much more frequent and successful, as it better served the finances of the construction companies.
Francisco Mangado and Andrea Deplazes, architects for whom construction – matter – is at the heart of architecture, are aware of the complex and contradictory history of industrialization in modern architecture. That is why, from the very first exchange of ideas, they avoid falling back on old clichés. They do not aspire to return to the old program of heroic industrialization. They disbelieve the maximalist aims of ‘hard’ prefabrication. And they recognize themselves neither in the cold aesthetics of the module nor in the rigidity of the industrial product conceived in its raw form. But they do share the optimism of the Zeitgeist: the hope that new technology, passed through the traditional tools of the architect – of the discipline – can be useful not only to improve the quality of our buildings and mitigate environmental deterioration, but also to establish better living conditions and guarantee the future of architecture.
Question (Q): What do we talk about today when we talk about ‘industrialization’?
Answer (A): When architects use the word ‘industrialization,’ they evoke very broad meanings, but almost all of them are vague, imprecise. They think of calculation, of rationalization of the module. They think of design optimization and production optimization. They think of speed and efficiency. Basically, they are thinking of a concept that is nothing more than the extension of another, older concept, ‘prefabrication,’ as old as construction itself but which we tend to associate with the Industrial Revolution. While they still make sense, all these meanings are so generic and culturally weighted that they have largely outlived their usefulness. This is why it is necessary to rethink the concept, to give it a precise content, especially in the context in which we live, marked by increasing environmental deterioration, the economic and social crisis, and another no less important crisis, that of the profession.
Q: How does the current context determine the idea of industrialization?
A: It shapes it in many ways, but rather than ‘determinism,’ it would be better to speak of ‘possibilism,’ in the sense that today's context offers new opportunities. Let's start with technology. It is clear that contemporary industrialization, hand in hand with robotics, will bring major changes to the world of construction, as it has already done in almost all areas of production, from car manufacturing to software. There will be changes in structural materials, in finishes, even in architectural types and in the way land is occupied. All of this will have a profound effect on the profession. This coming reality, far from being a problem, should be seen as a great opportunity which, like any great technological leap, will have profound economic, social, and cultural consequences.
Q: Is robotics a panacea?
A: It is not a panacea, in the sense that it will not solve our problems by itself. But it is an indispensable tool when it comes to thinking about the future – actually, the present – of architecture. Broadly speaking, we can say that robotic construction has the virtues that during the 20th century were associated with the concept of ‘industrialization,’ but not its disadvantages. In the short term, robotics reduces construction times, to the same extent that it improves quality, and we should think that, in the medium term, it will also make it possible to reduce costs, with all that this may entail from an economic and social point of view. Because of its ability to ‘place material’ with the greatest precision and in the optimum quantity, robotics is also the flexible tool with which we can research new ways of using materials, whether conventional ones or others that have so far not been able to have the relevance they deserve. This type of research is, in fact, one of the researches that the BAI Institute intends to undertake in order to give shape, within a reasonable timeframe, to construction systems that are, in every sense, more efficient and that can be standardized and successfully applied in reality. The important thing is that new technologies – in this case robotics – are not seen as a threat – that is, as something imposed from outside the world of design – but as a real project tool.
Q: But Mario Carpo has pointed out that robotics, and in general what is called ‘parametric design,’ can pose a threat to the concept of authorship that architects have been dealing with since the time of Alberti.
A: All paradigm shifts involve risks that need to be faced or combated, and indeed parametric design or digital craftsmanship can bring with it the unwanted transformation of what we understand an ‘architect’ or in general an ‘author’ to be, in that it can inspire impersonal, technocratic, and only apparently participatory ways of designing our environments. But this does not detract from the argument that we, as a profession, must appropriate the new technologies; in fact, it reinforces it, for a process of digitalization in which designers, authors, participate from within, will always be better, more moderate, more oriented, richer and more humanistic than one that is simply imposed on them from outside, technocratically. The architecture of the future will be digital or will not be, but in any case it will have to continue to be a culturally relevant, humanistic architecture.
Q: To what extent will robotization make it possible to overcome the old dilemmas that limited the development of traditional industrialization?
A: We must insist, once again, that robotics is not a panacea. Robotics will be useful, it will change things for the better, only to the extent that we know how to turn it into an effective design tool. However, robotics itself, as a tool, has a great virtue: it does not depend on mass production and the rigid model of typification on which the ‘classic’ factories of Taylorism depended. On the contrary, robotization today makes it possible to produce singular, unique, ad hoc objects without any disadvantages in terms of speed and quality of execution. And it is not just a matter of robotic arms working like highly skilled operators who are dedicated to the production of serial or unique objects; it is also a matter of these robotic arms being able to have a sort of brain, or rather a digital interface, which communicates immediately with the designer, so that the intermediate steps, the logistical mediations, between design and production are reduced. This implies an unprecedented potential: that robotized manufacture could become a kind of new craft, the ‘digital craft’, which on the one hand would be efficient in the broadest sense of the word and on the other hand would be specific or contextual in the sense that we architects give to the term. With this, we could break, for the first time in modernity, the old dilemma between mass production and designing specific objects.
Q: What will be the relationship of this new digital architecture with context?
A: Context determines, to a large extent, the specific character, linked to each place and each material culture, of a building. However, context, in the context of robotization and digital craftsmanship, can be understood in several ways. Context is, first of all, the environment in which we live, and in this respect robotization is a manufacturing process with great advantages. Only industrial processes in general, and digital craftsmanship in particular, allow us to accurately define the productive output, the amount of material and energy we consume in the process, the efficiency of the means-end relationship. This is related, in parallel, to the circular economy, since the determination of the material used and the energy consumed in the construction of the building is a prerequisite for the calculation of its life cycle. Moreover, robotic construction, which is cleaner and more precise than conventional construction, makes it possible to think of buildings in the long term: to anticipate their dismantling and recycling. And the cycle of advantages does not end here, as the new robotic techniques make it possible to use recycled materials –plastics, cardboard, even concrete – which traditional techniques have not been able to exploit. If we think in terms of recycling and circular economy, we are thinking in a different context: using local resources. Hence, robotization is also a way of taking into account, from new budgets, the local reality.
Q: One of the problems that has always plagued traditional industrialization has been precisely its inability to attend to the specific: the fact that it has been subordinated to the generic forms of mass production.
A: That has been the traditional trend, no doubt, but today any system of industrialization that wants to have a future, to be truly relevant, must take context into account. Not only in terms of the use of local materials, but also in an economic, social, and cultural sense. Economically, because counting on nearby resources is a way of sustaining traditional enterprises and encouraging new ones. Socially, because working in favor of the context means having local labor and, in the event that it is scarce or non-existent, encouraging training in new professional areas. In this sense, the new industrialization tools have huge potential as catalysts: they increase the speed of processes that are underway but are still incipient. What is interesting is that these catalysts can also be cultural, either because they resonate with the building traditions – with the material culture – of each place, or because they create new discourses, new narratives, capable of bringing together diverse impulses.
Q: Is industrialization also an ideological battle?
A: It is ideological in the broad sense of the term. Firstly, because robotization is now part of our environmental concerns, so that associating industrialization with sustainability is not only a way of improving the way we produce, pollute or manage our resources; it is also a way of establishing a necessary and attractive discourse, especially for young people. The battle of industrialization is ideological, on the other hand, because it affects the way architects and designers in general understand authorship: because it forces us to rethink what we are willing to give up and what we are not. It has a profound effect on the idea we have of our profession. And it is ideological, finally, because the whole thing depends, in the end, on a fundamental question: ‘Industrialization, what for?’ A question that has an almost political status.
Q: What is industrialization for, then?
A: First and foremost, to improve architecture. Industrialized processes cannot imply – as happened in the past – an undermining of excellence or of the architect's creative possibilities. Quite the opposite: they must ensure that excellence is as widely distributed as possible, and that creativity is channelled into viable and therefore effective currents, either because they are associated with the most relevant technologies or because they meet the real needs of society. This is why the improvement of architecture through contemporary industrialization is a way of putting up a fight in the social sphere as well. Improving architecture through efficiency but also through beauty is just another way of improving the conditions in which we live, improving society.
Q: Does industrialization have a ‘social conscience’?
A: It does, insofar as it can be a factor in improving architectural and urban quality, but above all insofar as it can make a major contribution to reducing social differences. For example, wouldn't it be desirable to take advantage of the benefits of robotic construction to work in the countryside and in peri-urban areas, two areas plagued by housing problems? In this respect, social rental housing could be an interesting and fruitful laboratory for experimentation. But there is another aspect that is even more relevant when talking about the social side of industrialization; an aspect that, once again, has to do with a question of unavoidable ideological, if not directly political, significance: to whom will the benefits of contemporary industrialization, cost savings, and increased quality ultimately go? We think they should go, above all, to the users of architecture, to citizens. Industrialization can in no way be a pretext for the exclusive benefit of real estate agents and builders.
Q: Are there ways to ensure that industrialization does not simply become an excellent new business opportunity?
A: Industrialization will be a business to the extent that architecture is also a business, because private development is about profit. However, the question is not so much whether industrialized architecture will remain as profitable as before, but to what extent, while remaining profitable, it will be able to benefit wider sections of the population. There is one area where industrialization can certainly make a difference, if taken responsibly: the labor market. Traditional construction, a degenerate variant of the craftsmanship of yesteryear, has led to a regrettable fact: the lack of skilled workers, of specialists. The inertia of the processes, the fact of having abundant, cheap, and untrained labor, the obtaining of large short-term profits linked to the tendering system, are all factors that have contributed to the perpetuation of ways of working that would otherwise have disappeared long ago. In contrast to the precariousness of pseudo-craft work, industrialization offers better qualified, much more technical and therefore more stable and better paid jobs, which will undoubtedly have an impact on society, especially in a country like Spain, which has largely lost its once rich craft traditions. So, with the most appropriate areas of research and projects, industrialization could help to smooth the transition between the conventional model based on unskilled labor and the new model based on greater technical training. This is just another way of saying that it will contribute to bridging the gap between traditional work and the new digital work, which today threatens the economic and social system on many fronts.
Q: Could it be said then that industrialization is being applied to reality at the same time as it is creating the mechanisms – ideological, economic, social – that make it possible?
A: Robotization, new industrialization, digital craftsmanship or whatever we prefer to call it, is not just a matter of technique. It spans diverse and intertwined dimensions; it implies, as you say, a system that is making itself as it is being tested in reality. Hence its complexity and the need to approach it with the right thinking and management tools. That is why it is so important to understand that industrialization, in order to be viable, to realize its full potential, must be sustained by training, by education. But an education that not only serves to train future designers in certain technical skills, but that, above all, serves to shape their thinking, to guide the way in which they will face the real problems of society.
Q: How does this type of education differ from traditional education?
A: It differs fundamentally in that it wants to remain polytechnic. Once powerful and even predominant, the polytechnic model has been diluted to the point where it is now almost an exception. Sometimes because the teaching traditions, more in tune with the artistic sides of the profession, have tended to favor the idea of the architect as a pure designer, as a specialist in forms. At other times because the demands of society, the ideology of fast architecture, and the crisis and confusion affecting the profession have undermined the polytechnic model of yesteryear. It is true that the training of an architect today can be neither that of a 19th century engineer nor that of a professional of the years of developmentalism or the Transition. But it is no less true that this should not imply renouncing the model. What polytechnic education needs is not a complete overhaul; it needs to be reformed, updated, and one of the ways to do this is to incorporate, from the outset, the technologies linked to the new industrialization. We can no longer separate the formal aspects of the discipline from the constructive aspects, unless we want to turn architects into mere ‘exterior designers’, as they already are to a large extent in other countries and cultural traditions.
Q: But how do you translate this into a curriculum, and are there precedents?
A: There are not many precedents beyond professional polytechnic models, with their advantages and disadvantages. In our case, the BAI Institute's polytechnic commitment has led us to focus primarily on the two areas where we think the impact could be greatest: on the one hand, postgraduate studies for architects and engineers; on the other, vocational training for future ‘digital artisans’ by recruiting people who have been left out of the job market or students who come from the baccalaureate and want to start learning by doing. This dual training will be closely linked to the Institute's research projects so that, from the outset, students can familiarize themselves with the new technological tools in the context of their actual application, i.e. by considering all the problems – functional, urban, economic, social, cultural – that architecture has to face. The spirit that inspires this educational project is none other than that of the tradition of pragmatism, Learn by Doing, which has inspired the most interesting pedagogies of the last century.
Q: So the Institute's training will be exclusively practical?
A: It won't be because the problem of contemporary industrialization is a complex, wide-ranging problem, in which all the factors that come together in architecture and which we professionals conventionally associate with the term ‘project’ must be taken into account. In fact, one of the singularities of BAI is that, without ceasing at any time to be an institute committed to technology – to high technology, strictly speaking – it also wants to be a teaching center in which theoretical or – to use a less pedagogically weighted word – ‘reflective’ knowledge plays a leading role. Thus, together with the design module which, in postgraduate education, will channel knowledge through real and concrete commissions, a series of very ambitious and diverse theoretical modules are proposed, which will enable students to understand, in all their complexity, the historical and current context in which the practices linked to new technologies must be inscribed. These modules will cover industrial techniques and processes, energy, and environmental sciences, without forgetting the humanities and social sciences, since any architect, engineer or designer must be aware of the relationship between the history of architecture and the history of construction, and understand society as a very complex web of interrelated knowledge.
Q: To what extent will companies and industrialists be involved in this educational project?
A: The BAI Institute, promoted by architecture professionals and supported by the Government of Navarre, the Ministry of Transport, Mobility, and Urban Agenda, and the Fundación Arquitectura y Sociedad, is conceived as an open forum, given the open and transversal nature of architecture and technology. A forum where architects, academia, government and, of course, industry can meet, exchange ideas and work together on specific projects. One of the fundamental objectives of BAI is, in this sense, to update the modern debates – think of the Werkbund, the Bauhaus – on the concurrent role of designers, industrialists, craftsmen, and users. To this end, we will count on the involvement of major national and international companies, whose knowledge, activated through ‘learning by doing’ and the ‘school-study’ concept, may lead to effective but viable solutions, even patents. BAI's educational project does not aim to perpetuate itself endogamically, tautologically, as is the case to a large extent in conventional universities. It does not wish to detach itself from real problems, but, on the contrary, to become fully involved with reality, to understand it, to transform it by relying on it. This is BAI's ultimate goal, and it is so because we believe that the ultimate goal of architecture is the same: to improve people's lives.